Benefits of One-Stop ODM Solutions
Strong relationships and a reliable supply chain with suppliers
- KingDa’s suppliers are carefully selected based on their ability to meet our high standards for quality, reliability, and ethical business practices. We work closely with them to understand their capabilities and processes and to develop a mutual understanding of our needs and expectations. This allows us to make informed decisions about sourcing and to work collaboratively to optimize our supply chain.
- We believe that strong supplier relationships are not only essential for ensuring the quality and reliability of our products but also for driving innovation and continuous improvement. By working closely with our suppliers, we are able to identify opportunities for process improvements, cost savings, and new product development.
- Ultimately, our goal is to build long-term partnerships with our suppliers that are based on mutual benefit and shared success. We believe that this approach creates a win-win situation for both our company and our suppliers, and we are committed to investing in these relationships to ensure our continued success.
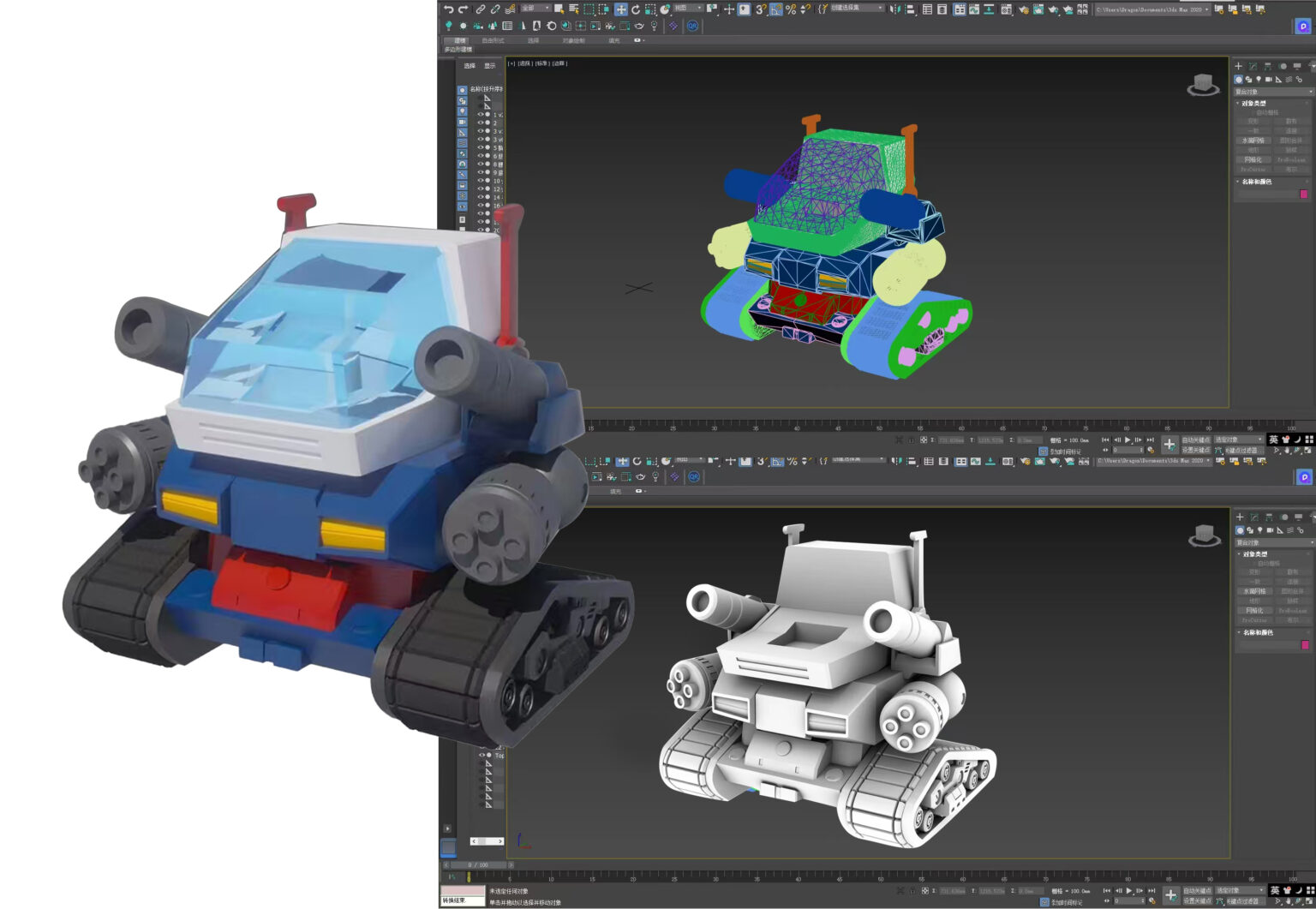

Toy & Collectible Manufacturing
We design and produce toys, collectibles and happiness for clients, fans and collectors….
Our "One Stop Solution" service
- KD International Limited’s one-stop solution is a comprehensive service that provides customers with everything they need in one place. It is a convenient and efficient way to meet all of our customers’ needs without having to go to multiple providers or sources.
- In our one-stop solution service, customers can expect to find a wide range of products and services that are tailored to their specific needs. These may include consulting, design, procurement, installation, maintenance, and repair services. We should be able to offer a range of options and solutions to meet different budgets and requirements. We provide customers with a seamless and hassle-free experience. This includes fast and reliable delivery services and responsive customer support.
- Another important aspect of a good one-stop solution service is quality assurance. The service provider should be committed to providing high-quality products and services that meet or exceed industry standards. They should also offer warranties or guarantees on their products and services to give customers peace of mind. Overall, a good one-stop solution service should be customer-focused, convenient, efficient, and of high quality. It should provide customers with a single point of contact for all of their needs, and make it easy for them to get the products and services they need when they need them.
Prototyping Approaches
Our design teams and creative community include a diverse mix of artists, sculptors, engineers and craftsmen, with backgrounds in the toy, videogame, SFX and licensed products worlds. Different toys and collectibles require different approaches. We employ a mix of:
- Hand sketches and illustration
- Digital sculpting / 3D modeling
- Rapid prototyping / 3D printing / Stereolithography (SLA)
- Hand sculpting
- Molding and casting
- Airbrushing and hand brushing
- Hand patterning and sewing (for plush toys)
- Graphic design, package mockups and proofs
Toy Design Process
Our design process is iterative and fun, with review and approvals at each step. At a high level it includes:
Rough Illustrations / concept art
guides design and engineering decisions
Final Concepts
clean “final” toy sketches, with a draft color palette
Turnarounds & control art
series of illustrated views from multiple angles; serves as blueprints for our sculptors and engineers; finalizes color palette
Packaging Mockups
package design runs in parallel with prototyping; if your design team is handling package graphic design we’ll provide a template with all required elements
Prototype Modeling
physical prototyping begins via 3D modelling/CAD or by hand sculpting or patterning; first prototypes are uncolored and without branding, and made of different materials than final toy
Production-Ready Prototype
prototype with final engineering; any final tweaks are made to the 3D design or shape of the toy
Tooling & Molding
tools and molds are created and refined
Packaging Approval
final packaging copy & artwork are approved; UPC barcodes are assigned
Painted / Colored Prototype
for plastic toys this is also called the “paint master”, and serves as paint guidelines for production; for plush this is a final sample in final dyed materials
Test Toys
Also called “engineering pilots” or “trial samples”, these are first samples in final materials; some of these may be unpainted/uncolored (for plastic toys, these are called “first shots”)
Packaging and Artwork Proof
proofs and/or packaging prototypes
Final Toy Samples (“Pre-Production Samples” or “Production Samples”)
final samples of the toy in its packaging; our clients receive, play with and approve the final toy samples before we start production
Quality Control
during production, our design team plays an active part in QC, ensuring final products achieve design goals and are consistent with the final toy samples – that is, we’re truly getting all the little details right during production
Review & Approvals
- At several prototyping stages we ask our clients to look at photos or samples of the prototype, give feedback, and request any improvements. We only proceed to the next prototyping stage when the current stage is right and your team (happily!) approves it.
- Production only begins when your team approves the final toy samples.
- Final toys & collectibles are consistent with the approved samples. We train our production and QC teams, and do multiple QC reviews and inspections at all phases of production. We also have independent third-party inspectors verify that we’re meeting our stringent toy quality targets.